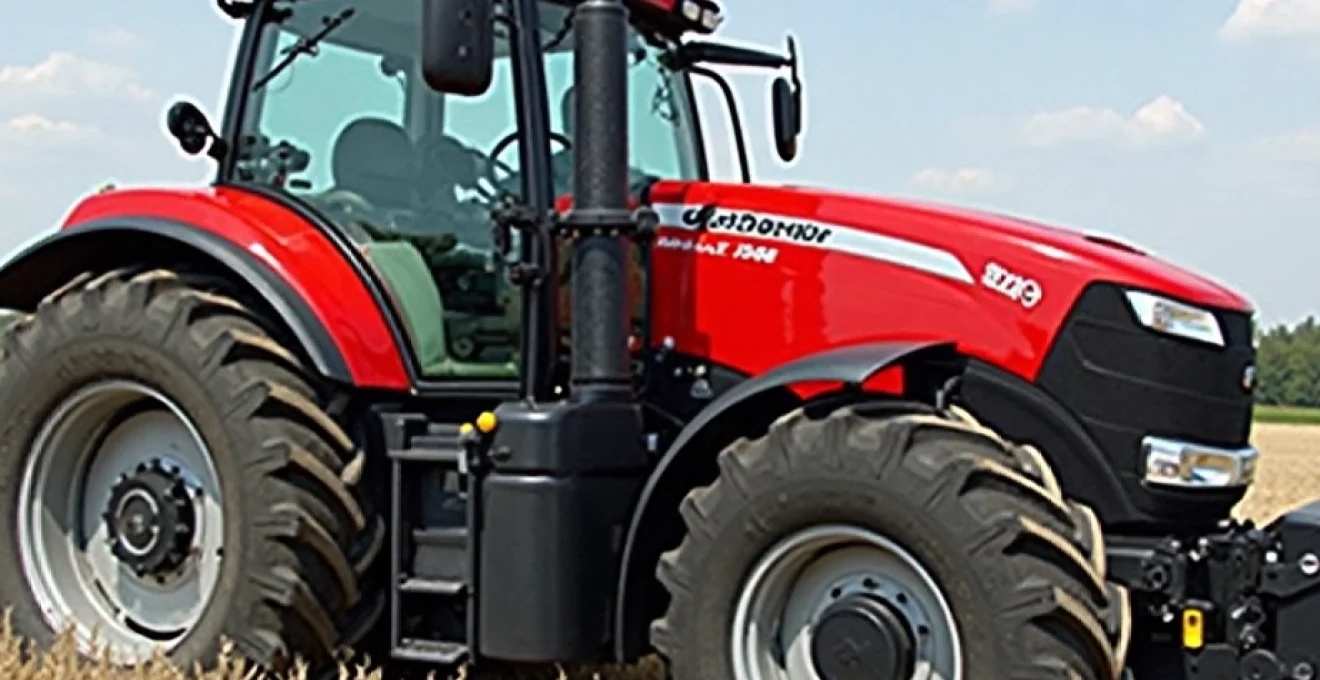
Le réglage précis du stabilisateur de bras de relevage sur un tracteur est essentiel pour optimiser les performances et la sécurité lors des travaux agricoles. Ce système complexe joue un rôle crucial dans le contrôle et la stabilité des outils attelés, influençant directement l’efficacité et la qualité du travail au champ. Une configuration adéquate permet non seulement d’améliorer la précision des opérations, mais aussi de réduire l’usure du matériel et la consommation de carburant. Comprendre les principes mécaniques et les composants clés du stabilisateur est la première étape vers une utilisation optimale de votre tracteur.
Principes mécaniques des stabilisateurs de bras de relevage
Les stabilisateurs de bras de relevage reposent sur des principes mécaniques sophistiqués visant à maintenir l’outil attelé dans une position stable et contrôlée. Le système fonctionne en contrebalançant les forces exercées sur l’outil pendant le travail, assurant ainsi une profondeur constante et une trajectoire précise. Cette stabilisation dynamique s’adapte en temps réel aux variations du terrain et aux efforts subis par l’outil.
Le principe fondamental repose sur l’équilibre entre la force hydraulique du relevage et la résistance du sol. Les stabilisateurs utilisent des systèmes de capteurs et de vérins hydrauliques pour ajuster continuellement la position de l’outil. Cette régulation permet de maintenir une pression constante sur le sol, essentielle pour des opérations telles que le labour ou le semis de précision.
L’efficacité du stabilisateur dépend de sa capacité à réagir rapidement aux changements de conditions. Par exemple, lors du passage sur une zone plus compacte du champ, le système doit immédiatement ajuster la pression hydraulique pour maintenir la profondeur de travail souhaitée. Cette réactivité est cruciale pour assurer une qualité de travail homogène sur l’ensemble de la parcelle.
Composants clés d’un stabilisateur de tracteur
Un stabilisateur de bras de relevage moderne est composé de plusieurs éléments essentiels, chacun jouant un rôle spécifique dans le fonctionnement global du système. La compréhension de ces composants est fondamentale pour effectuer des réglages précis et maintenir des performances optimales.
Vérins hydrauliques et leur fonctionnement
Les vérins hydrauliques sont le cœur du système de stabilisation. Ils transforment la pression hydraulique en mouvement mécanique, permettant d’ajuster la position des bras de relevage avec précision. Ces vérins sont capables de réagir rapidement aux commandes du système de contrôle, assurant une stabilisation en temps réel de l’outil attelé.
Le fonctionnement des vérins repose sur le principe de Pascal : la pression exercée sur un fluide incompressible se transmet intégralement dans toutes les directions. Dans le contexte d’un stabilisateur, cela se traduit par une capacité à exercer des forces importantes tout en maintenant une grande sensibilité aux ajustements fins. La pression hydraulique dans les vérins est constamment régulée pour s’adapter aux conditions de travail changeantes.
Système de contrôle électronique EHR (electronic hitch control)
Le système EHR est le cerveau du stabilisateur. Il analyse en permanence les données provenant des capteurs et ajuste le comportement des vérins hydrauliques en conséquence. Ce contrôle électronique permet une précision et une réactivité impossibles à atteindre avec des systèmes purement mécaniques.
L’EHR intègre des algorithmes sophistiqués qui prennent en compte de multiples paramètres tels que la vitesse du tracteur, la profondeur de travail souhaitée, et les caractéristiques du sol. Ces calculs complexes se traduisent par des ajustements en temps réel du relevage, assurant une stabilité optimale de l’outil dans toutes les conditions.
Capteurs de position et de force
Les capteurs sont les yeux et les oreilles du système de stabilisation. Ils fournissent des informations cruciales sur la position des bras de relevage et les forces exercées sur l’outil. Les capteurs de position, généralement de type potentiométrique ou magnétique, mesurent avec précision l’angle et la hauteur des bras de relevage.
Les capteurs de force, quant à eux, évaluent la résistance du sol et les efforts subis par l’outil. Ces données sont essentielles pour que le système EHR puisse réagir de manière appropriée aux variations de conditions de travail. Par exemple, une augmentation soudaine de la force mesurée peut indiquer le passage sur une zone plus compacte du champ, nécessitant un ajustement immédiat de la position de l’outil.
Accumulateurs hydrauliques et amortisseurs
Les accumulateurs hydrauliques et les amortisseurs jouent un rôle crucial dans l’absorption des chocs et la réduction des vibrations. Ces composants agissent comme des tampons entre le tracteur et l’outil attelé, améliorant le confort de conduite et réduisant l’usure mécanique.
Les accumulateurs stockent de l’énergie hydraulique sous forme de pression, permettant une réaction rapide aux variations de charge sans solliciter constamment la pompe hydraulique principale. Cette caractéristique est particulièrement utile lors des transitions rapides entre différentes conditions de sol. Les amortisseurs, quant à eux, dissipent l’énergie des mouvements brusques, contribuant à une stabilité accrue de l’ensemble tracteur-outil.
Procédure de réglage du stabilisateur
Le réglage optimal d’un stabilisateur de bras de relevage nécessite une approche méthodique et une compréhension approfondie du système. Une procédure bien exécutée peut significativement améliorer les performances du tracteur et la qualité du travail réalisé.
Diagnostic initial et inspection visuelle
Avant tout ajustement, il est crucial de procéder à un diagnostic complet du système. Cette étape commence par une inspection visuelle minutieuse de tous les composants du stabilisateur. Vérifiez l’état des vérins hydrauliques, des connexions électriques des capteurs, et des articulations mécaniques. Recherchez des signes d’usure excessive, de fuites hydrauliques, ou de dommages apparents.
Ensuite, effectuez un test de fonctionnement à vide pour évaluer la réactivité du système. Observez le comportement des bras de relevage lors de mouvements lents et rapides. Des mouvements saccadés ou une réponse lente peuvent indiquer des problèmes nécessitant une attention particulière avant de procéder aux réglages fins.
Ajustement de la sensibilité du système EHR
La sensibilité du système EHR détermine sa réactivité aux variations de charge et de position. Un réglage trop sensible peut entraîner des oscillations constantes, tandis qu’un réglage trop peu sensible peut compromettre la précision du travail. L’ajustement optimal dépend du type d’outil utilisé et des conditions de travail.
Pour régler la sensibilité :
- Commencez par un réglage moyen et testez le comportement du système en conditions réelles.
- Observez la stabilité de l’outil pendant le travail. Si l’outil oscille excessivement, réduisez progressivement la sensibilité.
- Si la réponse est trop lente aux variations du terrain, augmentez légèrement la sensibilité.
- Répétez ces ajustements jusqu’à obtenir un comportement stable et réactif de l’outil.
Calibrage des capteurs de position
Un calibrage précis des capteurs de position est essentiel pour garantir que le système EHR reçoit des informations exactes sur la position des bras de relevage. Cette étape est particulièrement importante après toute intervention mécanique sur le système de relevage.
La procédure de calibrage varie selon les modèles de tracteurs, mais suit généralement ces étapes :
- Placez les bras de relevage en position basse maximale.
- Activez le mode de calibrage via l’interface de contrôle du tracteur.
- Suivez les instructions pour définir les positions haute et basse maximales.
- Vérifiez que les valeurs affichées correspondent aux positions réelles des bras.
Un calibrage précis assure que le système EHR peut contrôler l’outil sur toute sa plage de mouvement avec précision.
Réglage de la pression hydraulique
La pression hydraulique dans le système de stabilisation influence directement la force de maintien et la réactivité du relevage. Un réglage inadéquat peut entraîner une usure prématurée des composants ou une instabilité de l’outil attelé.
Pour ajuster la pression hydraulique :
- Consultez le manuel du tracteur pour connaître les plages de pression recommandées.
- Utilisez un manomètre pour mesurer la pression actuelle du système.
- Ajustez la valve de régulation de pression pour atteindre la valeur souhaitée.
- Testez le système sous charge pour vérifier que la pression reste stable.
Un réglage optimal de la pression hydraulique assure une réponse rapide du système tout en protégeant les composants d’une surcharge.
Tests dynamiques avec différents outils attelés
La phase finale du réglage consiste à effectuer des tests dynamiques avec différents outils attelés. Ces tests permettent de vérifier que les ajustements réalisés sont adaptés à diverses conditions de travail.
Procédez comme suit :
- Commencez par tester le système avec un outil léger, comme une herse.
- Observez le comportement de l’ensemble tracteur-outil sur différents types de terrain.
- Répétez le test avec des outils plus lourds, comme une charrue.
- Ajustez finement les paramètres du stabilisateur en fonction des observations.
Ces tests dynamiques permettent d’affiner les réglages pour obtenir des performances optimales avec une variété d’outils et de conditions de travail.
Optimisation pour différents types de travaux agricoles
L’optimisation du stabilisateur de bras de relevage pour différents types de travaux agricoles est cruciale pour maximiser l’efficacité et la qualité du travail. Chaque opération agricole présente des défis uniques qui nécessitent des ajustements spécifiques du système de stabilisation.
Réglages pour le labour profond
Le labour profond exige une configuration particulière du stabilisateur pour maintenir une profondeur constante tout en gérant des charges importantes. Pour optimiser le système pour le labour :
- Augmentez la sensibilité du contrôle d’effort pour réagir rapidement aux variations de résistance du sol.
- Réglez la pression hydraulique à un niveau élevé pour maintenir une force de pénétration suffisante.
- Ajustez les accumulateurs hydrauliques pour absorber les chocs lors du passage sur des obstacles.
Ces réglages permettent de maintenir une profondeur de labour constante même dans des conditions de sol variables, assurant une préparation uniforme du lit de semence.
Paramètres pour le semis de précision
Le semis de précision nécessite une stabilité exceptionnelle pour garantir un placement uniforme des graines. Pour optimiser le stabilisateur pour le semis :
- Réduisez la sensibilité du système EHR pour éviter des ajustements trop fréquents qui pourraient perturber la régularité du semis.
- Affinez le réglage des capteurs de position pour maintenir une hauteur de semis constante.
- Utilisez le mode de contrôle de position plutôt que le contrôle d’effort pour maintenir une profondeur de semis précise.
Ces ajustements contribuent à une distribution uniforme des semences, essentielle pour une levée homogène et un rendement optimal des cultures.
Configuration pour le transport de charges lourdes
Le transport de charges lourdes avec des outils semi-portés requiert une configuration spécifique du stabilisateur pour assurer la sécurité et le confort de conduite. Pour optimiser le système lors du transport :
- Activez le mode de amortissement de transport si disponible, pour réduire les oscillations.
- Augmentez la pression dans les accumulateurs hydrauliques pour une meilleure absorption des chocs.
- Réduisez la sensibilité du système EHR pour éviter des ajustements brusques pendant le déplacement.
Ces réglages améliorent la stabilité du tracteur lors du transport, réduisant le risque de balancement et améliorant la sécurité sur route.
Maintenance préventive du système de stabilisation
Une maintenance préventive régulière est essentielle pour garantir la fiabilité et la longévité du système de stabilisation. Un entretien adéquat permet non seulement de prévenir les pannes coûteuses, mais aussi de maintenir les performances optimales du tracteur au fil du temps.
Voici les points clés d’un programme de maintenance préventive efficace :
- Inspection visuelle régulière des composants hydrauliques pour détecter les fuites ou l’usure.
- Vérification et nettoyage des connexions électriques des capteurs et du système EHR.
- Lubrification périodique des articulations mécaniques du système de relevage.
- Contrôle et ajustement de la tension des chaînes ou câbles de relevage, si présents.
- Analyse régulière de l’huile hydraulique pour détecter les signes de contamination ou de dégradation.
Une attention particulière doit être portée aux signes
de contamination ou de dégradation précoce de l’huile hydraulique. Ces signes peuvent inclure une coloration anormale, la présence de particules métalliques, ou une odeur inhabituelle. Une huile dégradée peut compromettre les performances du système et accélérer l’usure des composants hydrauliques.
En outre, il est recommandé de procéder à un test de performance du système de stabilisation au moins une fois par saison. Ce test devrait inclure une vérification de la réactivité du système, de la précision des capteurs, et de la capacité de maintien de charge. Toute anomalie détectée lors de ces tests doit être adressée rapidement pour éviter des pannes potentielles en pleine saison de travail.
Innovations technologiques dans les stabilisateurs de tracteurs
Le domaine des stabilisateurs de bras de relevage connaît une évolution rapide, avec l’intégration de technologies de pointe visant à améliorer la précision, l’efficacité et la facilité d’utilisation. Ces innovations transforment progressivement la manière dont les agriculteurs interagissent avec leurs équipements et optimisent leurs opérations au champ.
Systèmes GPS intégrés pour l’auto-ajustement
L’intégration de systèmes GPS dans les stabilisateurs de tracteurs représente une avancée majeure. Ces systèmes permettent un ajustement automatique et précis de la position de l’outil en fonction de la topographie du terrain et des paramètres de travail prédéfinis. Comment cela fonctionne-t-il concrètement ?
- Le GPS fournit des données de position en temps réel avec une précision centimétrique.
- Ces données sont combinées avec une cartographie détaillée du champ, incluant les variations de relief et les zones de compaction.
- Le système EHR utilise ces informations pour ajuster automatiquement la hauteur et l’angle de l’outil, optimisant ainsi le travail sur l’ensemble de la parcelle.
Cette technologie permet non seulement d’améliorer la qualité du travail, mais aussi de réduire la fatigue de l’opérateur, qui n’a plus besoin d’ajuster constamment les réglages manuellement. De plus, l’utilisation du GPS facilite la création de rapports détaillés sur les opérations effectuées, utiles pour la traçabilité et l’optimisation des pratiques agricoles.
Intelligence artificielle et apprentissage automatique
L’intégration de l’intelligence artificielle (IA) et de l’apprentissage automatique dans les systèmes de stabilisation ouvre de nouvelles perspectives pour l’agriculture de précision. Ces technologies permettent au système de s’adapter et d’apprendre à partir des données collectées au fil du temps, améliorant continuellement ses performances.
Par exemple, un système équipé d’IA peut :
- Analyser les données historiques de performance pour prédire les ajustements nécessaires dans des conditions similaires futures.
- Optimiser les réglages en temps réel en fonction de multiples paramètres tels que la vitesse du tracteur, l’humidité du sol, et la résistance rencontrée.
- Identifier des motifs de comportement du sol et de l’outil qui échapperaient à l’observation humaine, permettant des ajustements plus fins et plus efficaces.
L’apprentissage automatique permet également au système de s’adapter aux préférences spécifiques de chaque opérateur, créant une expérience de conduite personnalisée et plus intuitive. Cette symbiose entre l’homme et la machine promet d’améliorer significativement l’efficacité et la précision des opérations agricoles.
Connectivité IoT pour le diagnostic à distance
L’Internet des Objets (IoT) révolutionne la maintenance et le diagnostic des systèmes de stabilisation. Grâce à des capteurs connectés, les données de performance et d’état du système peuvent être transmises en temps réel à des plateformes de surveillance à distance. Quels sont les avantages concrets de cette connectivité ?
- Détection précoce des anomalies : Les algorithmes analysent en continu les données pour identifier les signes avant-coureurs de pannes potentielles.
- Maintenance prédictive : Les interventions peuvent être planifiées de manière optimale, réduisant les temps d’arrêt et prolongeant la durée de vie des équipements.
- Assistance à distance : Les techniciens peuvent diagnostiquer et parfois même résoudre les problèmes sans se déplacer, réduisant les coûts et les temps d’intervention.
De plus, la connectivité IoT facilite les mises à jour logicielles à distance, permettant aux fabricants d’améliorer continuellement les performances et les fonctionnalités des systèmes sans nécessiter d’intervention physique sur le tracteur. Cette approche « over-the-air » assure que les agriculteurs bénéficient toujours des dernières avancées technologiques.
En conclusion, ces innovations technologiques dans les stabilisateurs de tracteurs ne sont pas seulement des gadgets high-tech. Elles représentent de véritables leviers d’amélioration de la productivité, de la précision et de la durabilité en agriculture. En permettant une gestion plus fine et plus réactive des opérations au champ, ces technologies contribuent à optimiser l’utilisation des ressources et à réduire l’impact environnemental de l’agriculture moderne.