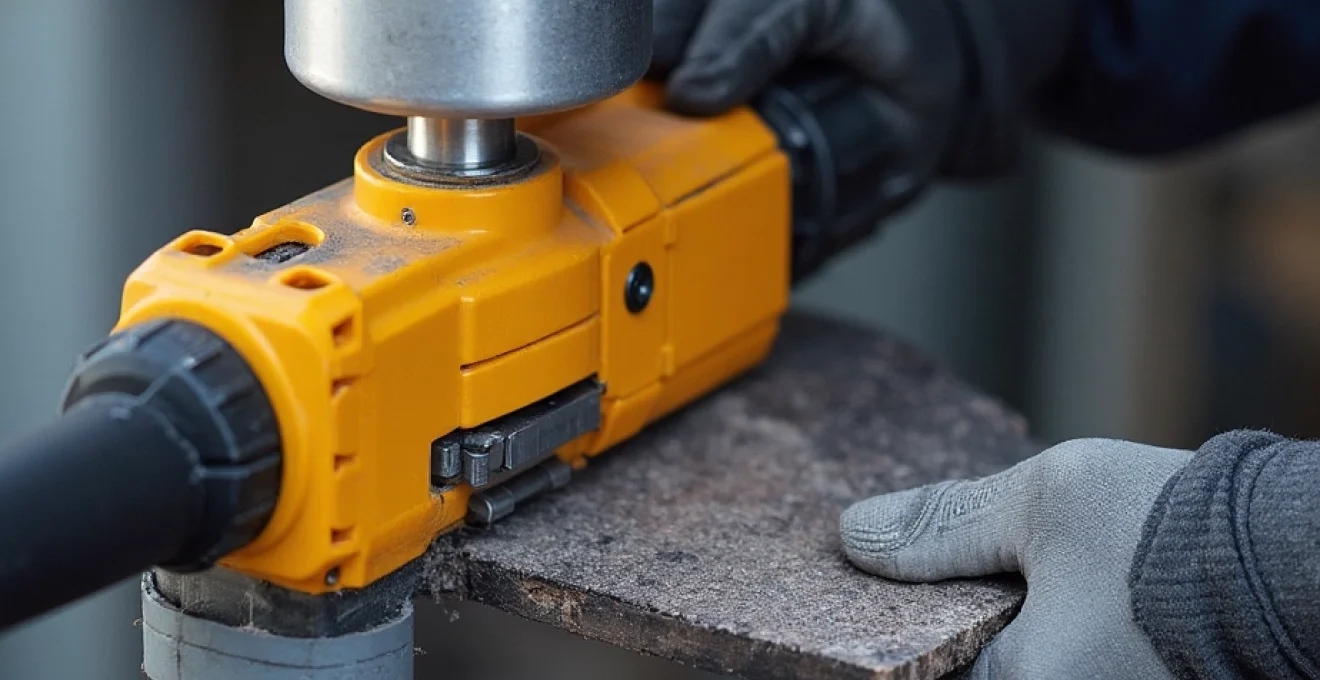
La sécurisation des outils est un aspect crucial dans de nombreux secteurs industriels, allant de l’usinage de précision à la fabrication à grande échelle. Un axe de blocage bien choisi et correctement installé peut faire toute la différence entre un processus de production fluide et efficace, et des arrêts coûteux dus à des défaillances d’outils. Comprendre les principes fondamentaux des axes de blocage, leurs types et applications spécifiques, ainsi que les critères de sélection appropriés, est essentiel pour optimiser la performance et la sécurité des équipements industriels.
Principes fondamentaux des axes de blocage pour outils
Les axes de blocage sont des composants mécaniques essentiels conçus pour maintenir fermement en place les outils de coupe, de perçage ou de fraisage sur les machines-outils. Leur fonction principale est d’assurer une fixation stable et précise, permettant ainsi d’obtenir des résultats d’usinage constants et de haute qualité. Ces dispositifs doivent résister aux forces considérables générées lors des opérations d’usinage, tout en facilitant le changement rapide des outils pour minimiser les temps d’arrêt.
Le principe de base d’un axe de blocage repose sur la création d’une liaison mécanique solide entre l’outil et la machine. Cette liaison peut être réalisée par différents mécanismes, tels que le serrage par friction, l’engagement de formes complémentaires ou l’utilisation de systèmes hydrauliques ou pneumatiques. L’objectif est toujours le même : éliminer tout jeu ou mouvement indésirable de l’outil pendant son utilisation.
Un aspect crucial des axes de blocage est leur capacité à maintenir l’alignement précis de l’outil par rapport à l’axe de rotation de la machine. Cet alignement est vital pour garantir la précision dimensionnelle des pièces usinées et pour prolonger la durée de vie des outils de coupe. Les systèmes de blocage modernes intègrent souvent des mécanismes d’auto-centrage qui assurent un positionnement optimal de l’outil à chaque montage.
Types d’axes de blocage et leurs applications spécifiques
Il existe une grande variété d’axes de blocage, chacun étant conçu pour répondre à des besoins spécifiques en termes de type d’outil, de machine et d’opération d’usinage. Comprendre les caractéristiques et les avantages de chaque type est essentiel pour choisir le système le plus approprié à une application donnée.
Axes de blocage à clavette pour outils rotatifs
Les axes de blocage à clavette sont largement utilisés pour les outils rotatifs tels que les fraises et les forets. Ce système utilise une clavette insérée dans une rainure de l’axe de la machine et de l’outil pour transmettre le couple. La clavette assure un alignement précis et empêche tout glissement de l’outil pendant l’opération.
Ces axes sont particulièrement adaptés aux applications nécessitant une transmission de couple élevée, comme l’usinage de matériaux durs. Leur conception simple les rend robustes et fiables, mais le changement d’outil peut être un peu plus long comparé à d’autres systèmes.
Les axes de blocage à clavette offrent une excellente résistance aux forces de coupe élevées, ce qui en fait un choix privilégié pour les opérations d’ébauche lourde.
Systèmes de bridage hydraulique pour fraiseuses CNC
Les systèmes de bridage hydraulique sont de plus en plus populaires dans les centres d’usinage CNC modernes. Ces dispositifs utilisent la pression hydraulique pour serrer l’outil contre le cône de la broche, créant ainsi une liaison extrêmement rigide et précise.
L’avantage majeur des systèmes hydrauliques est leur capacité à fournir une force de serrage uniforme sur toute la surface de contact. Cela se traduit par une meilleure concentricité de l’outil et une réduction des vibrations pendant l’usinage. De plus, ces systèmes permettent généralement un changement d’outil rapide et automatisé , ce qui est crucial pour la productivité dans les environnements de production à haut volume.
Dispositifs de serrage pneumatique pour tours
Les dispositifs de serrage pneumatique sont couramment utilisés dans les tours, en particulier pour les opérations nécessitant des changements d’outils fréquents. Ces systèmes utilisent l’air comprimé pour activer le mécanisme de serrage, offrant une solution rapide et efficace pour fixer les outils de tournage.
L’un des principaux avantages des systèmes pneumatiques est leur rapidité d’action. Le serrage et le desserrage de l’outil peuvent être effectués en quelques secondes, ce qui réduit considérablement les temps morts lors des changements d’outils. De plus, la nature propre de l’air comprimé en fait une option attrayante pour les environnements où la contamination par les fluides hydrauliques doit être évitée.
Mandrins à changement rapide pour perceuses
Les mandrins à changement rapide sont devenus la norme pour les perceuses modernes, tant dans les applications industrielles que grand public. Ces dispositifs permettent de changer les forets sans utiliser de clé, grâce à un mécanisme de serrage à ressort ou à cliquet.
La rapidité et la facilité d’utilisation sont les principaux avantages de ces mandrins. Ils sont particulièrement utiles dans les situations où l’opérateur doit fréquemment changer de taille de foret. Cependant, pour les applications nécessitant une très haute précision ou une grande force de serrage, des systèmes plus robustes peuvent être préférables.
Critères de sélection d’un axe de blocage adapté
Choisir le bon axe de blocage est crucial pour optimiser les performances de votre outil et assurer la sécurité de vos opérations. Plusieurs facteurs doivent être pris en compte pour faire le choix le plus judicieux.
Analyse des forces et couples en jeu
La première étape dans la sélection d’un axe de blocage est d’évaluer précisément les forces et les couples auxquels l’outil sera soumis pendant l’usinage. Cela inclut non seulement les forces de coupe directes, mais aussi les vibrations et les chocs potentiels.
Pour effectuer cette analyse, vous devez considérer :
- La nature du matériau à usiner (dureté, ductilité)
- Les paramètres de coupe (vitesse de rotation, avance)
- La géométrie de l’outil (diamètre, nombre de dents)
- Le type d’opération (perçage, fraisage, tournage)
Une fois ces données collectées, vous pouvez calculer les forces maximales attendues et choisir un axe de blocage avec une capacité de serrage supérieure à ces valeurs, en incluant un facteur de sécurité approprié.
Considérations de précision et répétabilité
La précision et la répétabilité du système de blocage sont cruciales pour maintenir la qualité des pièces usinées sur le long terme. Un axe de blocage de haute qualité doit assurer un positionnement constant de l’outil, avec des écarts minimaux entre les montages successifs.
Pour évaluer la précision d’un système de blocage, considérez :
- La concentricité maximale garantie
- La rigidité du système sous charge
- La stabilité thermique lors des cycles d’usinage
- La résistance à l’usure des surfaces de contact
Les systèmes offrant une précision de positionnement de l’ordre du micron sont généralement recommandés pour les applications de haute précision, telles que l’usinage de composants aérospatiaux ou médicaux.
Compatibilité avec les matériaux usinés
Le choix de l’axe de blocage doit également prendre en compte la nature des matériaux que vous prévoyez d’usiner. Certains matériaux, comme les alliages d’aluminium ou les plastiques, peuvent nécessiter des considérations spéciales en termes de force de serrage pour éviter la déformation de la pièce.
Pour les matériaux abrasifs ou corrosifs, il est important de choisir des axes de blocage avec des surfaces de contact résistantes à l’usure et à la corrosion. Des revêtements spéciaux ou des matériaux comme l’acier inoxydable peuvent être nécessaires dans ces cas.
La compatibilité chimique entre l’axe de blocage et les fluides de coupe utilisés est un aspect souvent négligé mais crucial pour la longévité du système.
Facilité de montage et démontage rapide
Dans un environnement de production, la rapidité des changements d’outils peut avoir un impact significatif sur la productivité globale. Les axes de blocage modernes offrent souvent des fonctionnalités de changement rapide qui permettent de réduire considérablement les temps d’arrêt.
Lors de l’évaluation de la facilité de montage et de démontage, considérez :
- Le temps nécessaire pour un cycle complet de changement d’outil
- La complexité du processus (nombre d’étapes, outils spéciaux requis)
- La possibilité d’automatisation du changement d’outil
- La robustesse du mécanisme face à des changements fréquents
Les systèmes de bridage hydraulique ou pneumatique offrent généralement les temps de changement les plus courts, mais ils peuvent nécessiter des investissements plus importants en termes d’infrastructure.
Techniques d’installation et d’alignement des axes de blocage
Une installation correcte et un alignement précis des axes de blocage sont essentiels pour garantir leur performance optimale et la longévité de vos outils. Voici quelques techniques clés à suivre :
- Nettoyage minutieux : Avant l’installation, assurez-vous que toutes les surfaces de contact sont parfaitement propres et exemptes de débris. Utilisez un solvant approprié et des chiffons non pelucheux.
- Inspection visuelle : Examinez attentivement l’axe de blocage et la broche de la machine pour détecter tout signe d’usure ou de dommage.
- Lubrification : Appliquez une fine couche de lubrifiant recommandé par le fabricant sur les surfaces de contact pour faciliter l’insertion et prévenir la corrosion.
- Insertion progressive : Insérez l’axe de blocage dans la broche avec précaution, en veillant à ne pas forcer. Un alignement correct devrait permettre une insertion en douceur.
- Vérification de la concentricité : Utilisez un comparateur pour vérifier la concentricité de l’axe de blocage par rapport à la broche. Ajustez si nécessaire.
Pour les systèmes de bridage hydraulique ou pneumatique, il est crucial de vérifier l’intégrité des joints et des conduites avant la mise en service. Toute fuite, même minime, peut compromettre la performance du système.
L’alignement précis est particulièrement important pour les axes de blocage utilisés dans des opérations de haute précision. Utilisez des outils de mesure calibrés et suivez les procédures recommandées par le fabricant pour obtenir les meilleurs résultats.
Maintenance préventive des systèmes de fixation d’outils
Une maintenance régulière et préventive des systèmes de fixation d’outils est essentielle pour maintenir leur performance et prolonger leur durée de vie. Un programme de maintenance bien structuré peut prévenir les pannes inattendues et réduire les temps d’arrêt coûteux.
Protocoles de nettoyage pour mandrins porte-fraise
Le nettoyage régulier des mandrins porte-fraise est crucial pour maintenir leur précision et leur fiabilité. Voici un protocole de nettoyage efficace :
- Démontez le mandrin selon les instructions du fabricant.
- Nettoyez toutes les pièces avec un solvant approprié pour éliminer les résidus d’huile et de copeaux.
- Utilisez de l’air comprimé filtré pour sécher et éliminer les particules restantes.
- Inspectez visuellement toutes les pièces pour détecter des signes d’usure ou de dommage.
- Lubrifiez légèrement les pièces mobiles avec un lubrifiant recommandé par le fabricant.
- Remontez le mandrin en veillant à ne pas introduire de contaminants.
Effectuez ce nettoyage au moins une fois par semaine pour les mandrins utilisés intensivement, ou selon les recommandations du fabricant.
Lubrification des mécanismes de serrage conique
La lubrification correcte des mécanismes de serrage conique est essentielle pour leur bon fonctionnement et leur longévité. Utilisez uniquement des lubrifiants spécifiés par le fabricant, car les lubrifiants inappropriés peuvent affecter la performance du serrage.
Voici quelques points clés à retenir pour la lubrification :
- Appliquez le lubrifiant en petite quantité, évitant tout excès qui pourrait attirer les contaminants.
- Assurez-vous que le lubrifiant pénètre bien dans tous les mécanismes mobiles.
- Respectez les intervalles de lubrification recommandés, qui peuvent varier selon l’intensité d’utilisation.
- Nettoyez soigneusement l’ancien lubrifiant avant d’appliquer le nouveau pour éviter les mélanges incompatibles.
Vérification de l’usure des surfaces de contact
L’inspection régulière des surfaces de contact est cruciale pour détecter les signes d’usure précoce qui pourraient compromettre la précision du serrage. Voici les points clés à vérifier :
- Examinez les surfaces pour détecter tout signe de piqûres, rayures ou déformations.
- Vérifiez l’uniformité de la surface de contact à l’aide d’un bleu de Prusse.
- Mesurez la concentricité et le faux-rond avec un comparateur de précision.
- Inspectez les filetages pour détecter tout signe d’usure ou de dommage.
Si vous constatez une usure excessive, il est important de remplacer les composants affectés rapidement pour éviter d’endommager les outils ou les pièces usinées.
Étalonnage des systèmes de mesure intégrés
De nombreux systèmes de fixation d’outils modernes intègrent des capteurs de force ou de position pour assurer un serrage optimal. L’étalonnage régulier de ces systèmes est essentiel pour maintenir leur précision. Voici quelques étapes clés pour l’étalonnage :
- Utilisez des instruments de référence certifiés pour vérifier la précision des capteurs.
- Suivez les procédures d’étalonnage spécifiées par le fabricant, généralement à intervalles réguliers.
- Documentez soigneusement tous les résultats d’étalonnage pour le suivi et l’assurance qualité.
- Ajustez ou remplacez les capteurs qui ne répondent pas aux spécifications de précision requises.
Un étalonnage régulier non seulement assure la précision du serrage, mais peut également aider à identifier les tendances d’usure avant qu’elles ne deviennent critiques.
Innovations technologiques dans les axes de blocage
Le domaine des axes de blocage pour outils connaît une évolution rapide, avec de nombreuses innovations visant à améliorer la précision, la fiabilité et l’efficacité des systèmes de fixation. Voici quelques-unes des avancées technologiques les plus prometteuses :
Systèmes de serrage intelligents
Les axes de blocage « intelligents » intègrent des capteurs avancés et des systèmes de contrôle électronique pour optimiser en temps réel la force de serrage. Ces systèmes peuvent ajuster automatiquement la pression de serrage en fonction des conditions d’usinage, assurant ainsi une fixation optimale tout en minimisant l’usure de l’outil et du porte-outil.
Les systèmes de serrage intelligents peuvent augmenter la durée de vie des outils jusqu’à 30% en adaptant dynamiquement la force de serrage aux conditions d’usinage.
Matériaux composites légers
L’utilisation de matériaux composites avancés dans la fabrication des axes de blocage permet de réduire significativement leur poids tout en maintenant, voire en améliorant, leur rigidité. Ces axes plus légers permettent des accélérations et des décélérations plus rapides, améliorant ainsi la productivité, particulièrement dans les applications d’usinage à grande vitesse.
Systèmes de refroidissement intégrés
Les nouveaux axes de blocage intègrent souvent des canaux de refroidissement sophistiqués qui permettent d’acheminer le liquide de coupe directement à travers l’axe et jusqu’au bord de coupe de l’outil. Cette technologie améliore considérablement l’évacuation des copeaux et la dissipation de la chaleur, permettant des vitesses de coupe plus élevées et une meilleure qualité de surface.
Interfaces de connexion sans contact
Les interfaces de connexion sans contact, utilisant des technologies comme l’induction magnétique ou la transmission de données optiques, commencent à remplacer les connexions mécaniques traditionnelles. Ces systèmes éliminent l’usure des contacts physiques et permettent une transmission plus rapide et plus fiable des données et de l’énergie entre la machine et l’outil.
Ces innovations technologiques ouvrent de nouvelles possibilités pour l’optimisation des processus d’usinage, promettant des gains significatifs en termes de précision, de productivité et de durée de vie des outils. Cependant, leur adoption nécessite souvent des investissements importants et une formation adéquate du personnel.
En conclusion, le choix et l’utilisation appropriés des axes de blocage sont essentiels pour garantir la sécurité, la précision et l’efficacité des opérations d’usinage. Une compréhension approfondie des différents types d’axes, de leurs applications spécifiques, et des critères de sélection permet de prendre des décisions éclairées pour optimiser les processus de production. La maintenance préventive et l’adoption des dernières innovations technologiques peuvent contribuer significativement à améliorer les performances et la longévité des systèmes de fixation d’outils, offrant ainsi un avantage compétitif dans un environnement industriel en constante évolution.