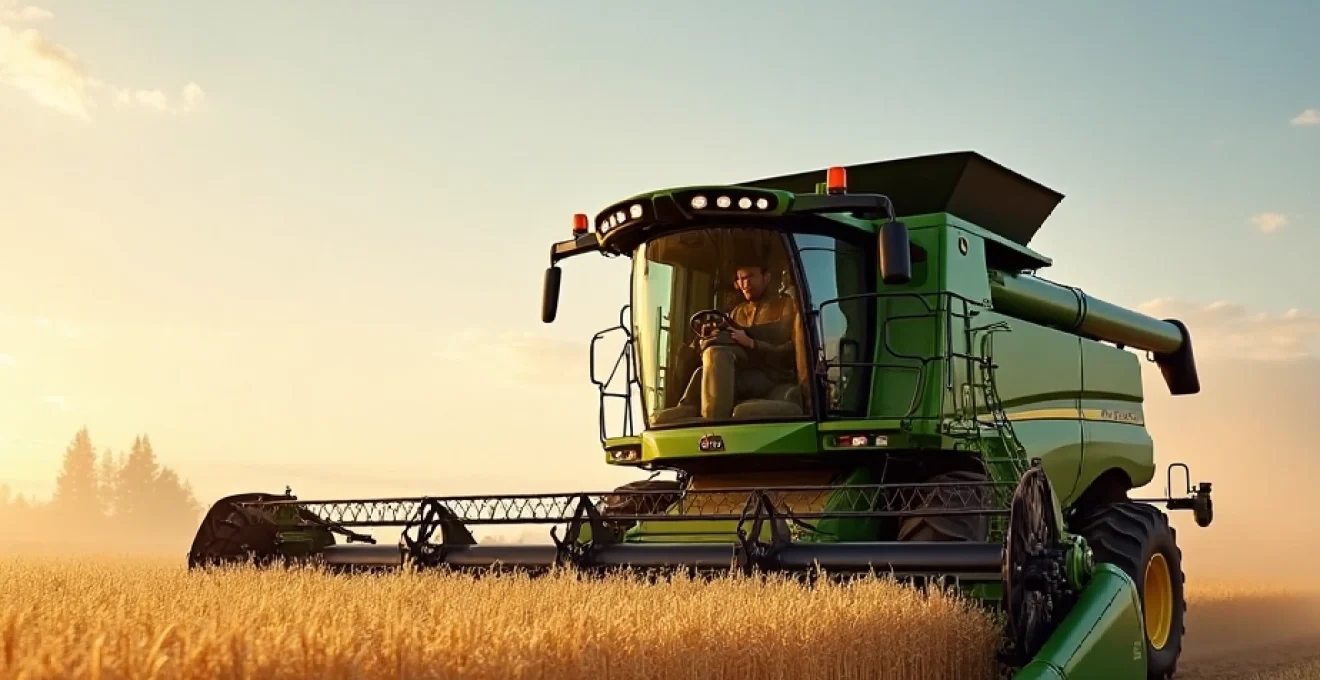
L’ensilage représente une étape cruciale dans la production fourragère, conditionnant la qualité nutritionnelle de l’alimentation du bétail pour toute une saison. Une ensileuse performante et correctement réglée est la clé d’une récolte optimale, permettant de maximiser le rendement tout en préservant la valeur nutritive des cultures. La précision des ajustements de la machine influence directement la qualité de la coupe, l’éclatement des grains et la conservation du fourrage. Maîtriser les subtilités du réglage d’une ensileuse est donc un savoir-faire essentiel pour tout agriculteur ou entrepreneur de travaux agricoles soucieux d’optimiser sa production fourragère.
Principes fondamentaux du réglage d’une ensileuse
Le réglage d’une ensileuse repose sur un équilibre délicat entre plusieurs paramètres interdépendants. La finesse de hachage, l’éclatement des grains et la régularité du flux de récolte sont les piliers d’un ensilage de qualité. Un réglage optimal permet non seulement d’obtenir un fourrage homogène et bien conservé, mais aussi de réduire l’usure de la machine et la consommation de carburant.
La première étape consiste à adapter les réglages au type de culture et à son stade de maturité. Un maïs plus sec nécessitera par exemple une coupe plus fine pour faciliter le tassement au silo. À l’inverse, une herbe jeune et humide demandera une longueur de coupe plus importante pour éviter les pertes par écoulement de jus.
L’objectif est d’obtenir un hachage régulier, avec des brins de longueur adaptée à la physiologie digestive des ruminants. Pour le maïs ensilage, on vise généralement une longueur théorique de coupe entre 8 et 12 mm. Cette finesse permet un bon tassement au silo tout en préservant une structure physique suffisante pour stimuler la rumination.
Un réglage précis de l’ensileuse est la garantie d’un fourrage de qualité, base d’une alimentation performante et économique du troupeau.
Au-delà de la coupe, l’éclatement des grains joue un rôle majeur dans la digestibilité de l’ensilage de maïs. Un grain intact traversera le système digestif sans être pleinement valorisé. L’objectif est donc d’obtenir au moins 95% de grains éclatés, avec une fragmentation en 4 à 8 morceaux pour les grains les plus matures.
Optimisation du système de coupe pour maximiser le rendement
Le cœur de l’ensileuse, son système de coupe, mérite une attention toute particulière. Son réglage conditionne non seulement la qualité du hachage, mais aussi les performances globales de la machine. Un système de coupe bien ajusté permet de maintenir un débit élevé tout en limitant la consommation d’énergie.
Ajustement précis de la longueur de coupe théorique (LCT)
La longueur de coupe théorique (LCT) est le premier paramètre à régler. Elle dépend du nombre de couteaux sur le rotor et de la vitesse d’alimentation. Pour ajuster la LCT, on joue principalement sur la vitesse des rouleaux d’alimentation. Plus ils tournent lentement par rapport au rotor, plus la coupe sera fine.
Il est important de noter que la LCT n’est qu’une valeur théorique. La longueur réelle des brins sera influencée par d’autres facteurs comme l’affûtage des couteaux ou la vitesse d’avancement de la machine. Un contrôle régulier de la longueur effective des brins est donc nécessaire pour affiner les réglages.
Affûtage et écartement des couteaux du rotor
Des couteaux bien affûtés sont essentiels pour obtenir une coupe nette et régulière. Un affûtage quotidien est recommandé, idéalement toutes les 4 à 5 heures de travail. L’affûtage permet non seulement d’améliorer la qualité de coupe, mais aussi de réduire la consommation de carburant et l’usure de la machine.
L’écartement entre les couteaux et le contre-couteau est tout aussi crucial. Un écartement trop important entraîne un écrasement plutôt qu’une coupe franche, tandis qu’un écartement trop faible augmente l’usure et les risques de casse. L’objectif est d’obtenir un fonctionnement comparable à celui d’une paire de ciseaux, avec un écartement idéal compris entre 0,1 et 0,3 mm.
Réglage du contre-couteau pour une coupe nette
Le contre-couteau joue un rôle essentiel dans la qualité de la coupe. Son réglage doit être effectué après chaque affûtage des couteaux du rotor. L’objectif est d’obtenir un effet de cisaillement optimal entre les couteaux mobiles et le contre-couteau fixe.
Un réglage précis du contre-couteau permet non seulement d’améliorer la qualité de coupe, mais aussi de réduire la consommation d’énergie. Un contre-couteau mal réglé peut entraîner une augmentation de la consommation de carburant de l’ordre de 10 à 15%.
Adaptation de la vitesse d’avancement à la densité de la récolte
La vitesse d’avancement de l’ensileuse doit être adaptée à la densité de la culture et aux conditions de récolte. Une vitesse trop élevée peut entraîner des bourrages et une coupe irrégulière, tandis qu’une vitesse trop faible réduit le débit de chantier.
L’objectif est de maintenir un flux de récolte constant et proche de la capacité maximale de la machine. Cela permet d’optimiser la qualité de coupe tout en maximisant le rendement. Les ensileuses modernes disposent souvent de systèmes automatiques d’adaptation de la vitesse en fonction du flux de récolte.
Configuration du système d’alimentation pour un flux constant
Le système d’alimentation de l’ensileuse joue un rôle crucial dans la régularité du flux de récolte et, par conséquent, dans la qualité du hachage. Un flux constant et bien maîtrisé est la clé d’une coupe homogène et d’un fonctionnement optimal de la machine.
Synchronisation des rouleaux d’alimentation avec la vitesse du rotor
La synchronisation entre les rouleaux d’alimentation et le rotor de coupe est essentielle pour obtenir la longueur de coupe désirée. Cette synchronisation se fait généralement via un variateur de vitesse qui permet d’ajuster finement la vitesse des rouleaux par rapport à celle du rotor.
Pour une longueur de coupe plus courte, on ralentit les rouleaux d’alimentation par rapport au rotor. À l’inverse, pour une coupe plus longue, on accélère les rouleaux. Il est important de vérifier régulièrement cette synchronisation, car elle peut être affectée par l’usure des composants ou les variations de conditions de récolte.
Ajustement de la pression des rouleaux selon le type de culture
La pression exercée par les rouleaux d’alimentation sur la récolte doit être adaptée au type de culture et à son taux d’humidité. Une pression trop faible peut entraîner une alimentation irrégulière, tandis qu’une pression excessive peut écraser la récolte et perturber le flux.
Pour une culture sèche comme du maïs à forte maturité, une pression plus importante sera nécessaire pour assurer une bonne préhension. À l’inverse, pour une herbe jeune et humide, une pression plus légère suffira. Certaines ensileuses modernes proposent des systèmes de réglage automatique de la pression en fonction du type de culture.
Optimisation de l’ouverture du bec cueilleur
L’ouverture du bec cueilleur doit être ajustée en fonction de la hauteur et de la densité de la culture. Une ouverture trop large peut entraîner des pertes par projection, tandis qu’une ouverture trop étroite risque de provoquer des bourrages.
Pour le maïs, l’objectif est de régler l’ouverture du bec de manière à ce que les épis soient cueillis juste en dessous de leur point d’attache. Cela permet de minimiser la quantité de tiges récoltées tout en assurant une collecte complète des épis.
Un système d’alimentation bien réglé est la garantie d’un flux de récolte régulier, condition sine qua non d’un hachage homogène et de qualité.
Paramétrage du système d’éclateur pour un traitement optimal des grains
L’éclateur de grains est un élément clé pour la valorisation de l’ensilage de maïs. Son rôle est de fragmenter les grains pour en améliorer la digestibilité. Un réglage précis de l’éclateur permet d’optimiser la valeur nutritive du fourrage tout en limitant les pertes d’énergie.
Réglage de l’écartement des rouleaux éclateurs
L’écartement entre les rouleaux éclateurs doit être ajusté en fonction du stade de maturité du grain. Pour des grains laiteux-pâteux, un écartement de 1 à 2 mm sera suffisant. Pour des grains plus matures et vitreux, il faudra réduire cet écartement jusqu’à 0,5 mm voire moins.
Il est important de vérifier régulièrement cet écartement, car l’usure des rouleaux peut le modifier au fil du temps. Un contrôle visuel de l’éclatement des grains dans le fourrage haché permet d’ajuster finement ce réglage.
Choix de la vitesse différentielle adaptée au stade de maturité
La vitesse différentielle entre les deux rouleaux éclateurs influence l’intensité de l’éclatement des grains. Pour des grains encore tendres, une différence de vitesse de 20% peut suffire. Pour des grains plus matures et durs, on pourra augmenter cette différence jusqu’à 30 ou 40%.
Ce réglage permet d’obtenir un effet de cisaillement plus ou moins prononcé sur les grains. L’objectif est d’atteindre un taux d’éclatement supérieur à 95%, avec une fragmentation en 4 à 8 morceaux pour les grains les plus matures.
Adaptation de la pression des rouleaux à l’humidité du grain
La pression exercée par les rouleaux éclateurs doit être adaptée à l’humidité du grain. Des grains plus humides nécessiteront une pression moindre pour être correctement éclatés, tandis que des grains secs et vitreux demanderont une pression plus importante.
Un réglage trop agressif sur des grains humides peut entraîner un écrasement plutôt qu’un éclatement, réduisant la qualité du fourrage. À l’inverse, une pression insuffisante sur des grains secs laissera passer trop de grains intacts.
Calibrage du système de projection pour une trémie bien remplie
Le système de projection, composé de l’accélérateur et de la goulotte d’éjection, joue un rôle crucial dans le remplissage homogène des remorques. Un réglage précis de ces éléments permet d’optimiser le débit de chantier tout en minimisant les pertes.
Ajustement de la vitesse de rotation de l’accélérateur
La vitesse de rotation de l’accélérateur doit être adaptée au type de culture et à la distance de projection souhaitée. Une vitesse trop élevée peut entraîner une usure prématurée des pales et une consommation d’énergie excessive. À l’inverse, une vitesse trop faible peut provoquer des bourrages et un remplissage irrégulier des remorques.
Pour le maïs ensilage, une vitesse périphérique de l’accélérateur comprise entre 45 et 55 m/s est généralement recommandée. Cette plage permet d’assurer une projection efficace tout en limitant la consommation d’énergie.
Orientation précise de la goulotte d’éjection
L’orientation de la goulotte d’éjection est essentielle pour un remplissage optimal des remorques. Elle doit être ajustée en fonction de la hauteur et de la position de la remorque par rapport à l’ensileuse. Un réglage précis permet de minimiser les pertes par projection et d’assurer un remplissage homogène.
Les ensileuses modernes disposent souvent de systèmes automatiques d’orientation de la goulotte. Ces dispositifs permettent d’ajuster en continu la direction du jet en fonction du déplacement de la remorque, optimisant ainsi le remplissage.
Réglage de la distance de projection selon le gabarit de la remorque
La distance de projection doit être adaptée au gabarit de la remorque utilisée. Une projection trop courte entraînera des pertes au sol, tandis qu’une projection trop longue risque de faire passer le fourrage par-dessus la remorque.
Le réglage de la distance de projection se fait généralement en ajustant la vitesse de rotation de l’accélérateur et l’inclinaison de la casquette en bout de goulotte. L’objectif est d’obtenir un jet puissant mais contrôlé, permettant un remplissage homogène de la remorque du front à l’arrière.
Maintenance préventive pour des performances optimales
Une maintenance régulière et préventive est essentielle pour garantir les performances et la longévité de l’ensileuse. Elle permet non seulement d’éviter les pannes coûteuses en pleine saison, mais aussi de maintenir la qualité de coupe et l’efficacité énergétique de la machine.
Protocole d’inspection quotidienne des composants critiques
Une inspection quotidienne des principaux composants de l’ensileuse est primordiale. Elle doit inclure la vérification de l’état des
couteaux du rotor, du contre-couteau et des rouleaux éclateurs. Il convient également de contrôler la tension des courroies, le niveau des fluides et l’état général des composants mécaniques.
Une attention particulière doit être portée aux systèmes de sécurité, notamment le détecteur de métaux. Son bon fonctionnement est crucial pour éviter les dommages au rotor de coupe en cas d’intrusion d’un corps étranger métallique.
Calendrier de remplacement des pièces d’usure
Certaines pièces de l’ensileuse sont soumises à une usure importante et nécessitent un remplacement régulier. Il est recommandé d’établir un calendrier précis de remplacement basé sur les heures de fonctionnement ou la surface récoltée.
Les couteaux du rotor, par exemple, doivent être remplacés après environ 500 hectares de récolte ou lorsque leur longueur a diminué de 7 à 10 mm. Les rouleaux éclateurs, quant à eux, peuvent généralement fonctionner pendant 2000 à 3000 hectares avant d’être remplacés.
Un suivi rigoureux de l’usure des pièces permet d’anticiper les remplacements et d’éviter les pannes en pleine saison de récolte. Cela contribue également à maintenir les performances de la machine à leur niveau optimal.
Lubrification régulière des points de graissage
La lubrification régulière des nombreux points de graissage de l’ensileuse est essentielle pour prévenir l’usure prématurée des pièces mobiles et assurer un fonctionnement fluide de la machine. Un graissage quotidien des points les plus sollicités est généralement recommandé.
Il est important de suivre scrupuleusement les recommandations du constructeur concernant la fréquence de graissage et le type de graisse à utiliser pour chaque point. L’utilisation d’une pompe à graisse automatique peut faciliter cette tâche et garantir une lubrification plus régulière et homogène.
Une maintenance préventive rigoureuse est le meilleur garant de la fiabilité et de la longévité de votre ensileuse. Elle contribue directement à la qualité de votre récolte et à l’efficacité de votre chantier d’ensilage.
En conclusion, le réglage optimal d’une ensileuse est un processus complexe qui nécessite une attention constante et une bonne compréhension des interactions entre les différents paramètres de la machine. La clé réside dans l’adaptation fine des réglages aux conditions spécifiques de chaque chantier : type de culture, stade de maturité, taux d’humidité, etc.
Un réglage précis, associé à une maintenance préventive rigoureuse, permettra non seulement d’optimiser la qualité de votre ensilage, mais aussi de préserver votre machine et de réduire vos coûts de fonctionnement. N’hésitez pas à faire appel à des spécialistes ou à suivre des formations pour parfaire votre maîtrise de cet outil essentiel à la production fourragère moderne.